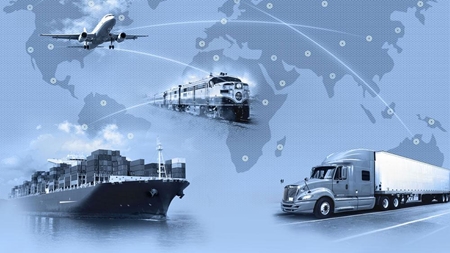
ساخت لبههای برش «الماسه» فوق سخت توسط محققان دانشگاه صنعتی امیرکبیر
به گزارش گروه فناوری خبرگزاری دانشجو، محققان دانشگاه صنعتی امیرکبیر برای نخستین بار در جهان موفق به ساخت لبههای برش (الماسه) فوق سخت تماما کامپوزیت سرامیکی شدند. بهزاد نایبی دانشآموخته دکتری مهندسی مواد، کامپوزیت دانشگاه صنعتی امیرکبیر و مجری طرح «تولید کامپوزیتهای سرامیکی فوق دما بالای تقویت شده با فازهای کاربیدی درجا به روش تفجوشی پلاسما جرقهای» گفت: تولید قطعات از سرامیکهای فوق دما بالا به روشهای ذوبی در دمای ذوب بیشتر از ۳۰۰۰ درجه سانتیگراد، تقریبا غیرممکن است. از این رو، روشهای مبتنی بر متالورژی پودر، تنها راه ممکن برای تولید این گروه از سرامیکها هستند که خود با چالشهای فناورانه گوناگونی مواجهند.
وی ادامه داد: افزون بر نیاز به کورههای پخت با دمای بیش از ۲۰۰۰ درجه سانتیگراد که بسیار گرانقیمت هستند، قطعات سرامیکی فوق دما بالای تولید شده به روش متالورژی پودر، معمولا خواص مکانیکی ضعیفی دارند که کاربردهای آنها را محدود میکند. کامپوزیتسازی، یکی از اصلیترین راهکارهای افزایش خواص مکانیکی این دسته کامپوزیتها است. از این رو در این پروژه تصمیم گرفته شد تا در گام نخست، از این راهکار برای غلبه بر خواص مکانیکی ضعیف قطعات، استفاده شود.
محقق دانشگاه امیرکبیر با اشاره به کامپوزیتهای سرامیکی طراحی شده در این پروژه اظهار کرد: این سرامیکها ترکیبی از سختی بسیار بالا، دیرگدازی، مقاومت به شوک حرارتی و پایداری شیمیایی را ارئه میدهند که کاربردهای بالقوه فراوانی را برای آنها، ایجاد میکند.
به گفته وی، این کامپوزیتها در صنایع هوافضای پیشرفته، سپرهای حرارتی و ابزارهای برش و ماشینکاری، کاربرد دارند.
وی با بیان اینکه تولید این سرامیکها به روشهای مرسوم متالورژی پودر، مستلزم بهکارگیری دماهای پخت بیش از ۲۰۰۰ درجه سانتیگراد است، تصریح کرد: این روشهای قدیمی از دیدگاه فناورانه، بسیار گرانقیمت هستند و صرفه اقتصادی ایجاد نمیکنند. همچنین، پخت این مواد در دماهای بیش از ۲۰۰۰ درجه سانتیگراد، با کاهش زیادی در چقرمگی شکست همراه است که کاربردهای قطعات را با چالش مواجه میکند.
دانشآموخته دانشگاه صنعتی امیرکبیر بیان کرد: این در حالی است که روش نوین پلاسما جرقهای قابلیت چگالسازی قطعات در دماهای پایینتر و زمانهای بسیار کوتاه را فراهم میکند. از این رو، روش یاد شده به عنوان راهکار دوم برای بهینهسازی ویژگیها و افزایش صرفه اقتصادی تولید، بهکار گرفته شد.
به گفته نایبی، بهکارگیری راهبرد تقویت با سنتز درجای فازهای کاربیدی، مهمترین جنبه نوآوری این پژوهش است که نه تنها افزایش چشمگیر خواص مکانیکی را سبب میشود، که به کاهش بیشتر دمای تفجوشی نیز کمک میکند. به بیان دیگر، در این پژوهش برای نخستین بار در جهان با در نظر گرفتن ترکیبی از سه راهکار یاد شده، قطعات ابزار برش (الماسههای تراش) از جنس کامپوزیتهای زمینه دیبورید زیرکونیم و دیبورید تیتانیم، با خواص برتر تولید شدهاند که مزیتهای گوناگونی را در مقایسه با قطعات مشابه از جنس دیگر مواد، فراهم میسازند.
وی تاکید کرد: روش بهکار گرفته شده در این پژوهش، قابلیت تولید کامپوزیتهای سرامیکی فوق دما بالا را در دماهای کمتر از ۱۸۰۰ درجه سانتیگراد فراهم میکند که با توجه به تکنولوژی موجود، به راحتی و با قیمت بسیار پایینتر، در دسترس است.
این محقق دانشگاه صنعتی امیرکبیر افزود: هزینه تمام شده قطعات در مقایسه با لبههای برش موجود در بازار، به شکل چشمگیری پایینتر و دوام قطعات، بسیار بالاتر است.
وی بیان کرد: مهمترین پیچیدگی طرح، جبران آثار کاهش دمای تفجوشی بود که طی آن، با تنظیم ترکیب و توزیع مواد اولیه در زمینه کامپوزیتی و نیز راهکار سنتز درجای فازهای تقویتکننده، نه تنها آثار مخرب کاهش دمای تفجوشی بر افت چگالی کامپوزیت جبران شد، که خواص مکانیکی به شکل چشمگیری ارتقاء یافت که در مقایسه با دادههای منتشر شده، رکوردی جهانی برای این مواد به شمار میرود.
نایبی افزود: با توجه به بررسیهای عملی و آزمونهای تجربی، قطعات تولید شده در این پژوهش چه از دیدگاه ویژگیهای عملکردی و چه از دیدگاه دوام و قابلیت تحمل شوکهای حرارتی و لرزش حین فرایند برش، جایگزین مناسبی برای ابزار فعلی به شمار میروند.
وی ادامه داد: در این پروژه، ساخت لبههای برش (الماسه) فوق سخت تماما کامپوزیت سرامیکی برای نخستین بار در جهان، به نتیجه رسیده است. این در حالی است که قطعات با کاربرد مشابه، یا از جنس الماس و کاربید تنگستن ساخته میشوند که بسیار گران قیمت هستند، یا با اعمال پوششهای سرامیکی بر فولادهای ابزار تولید میشوند که دوام آنها بسیار محدود است.
محقق دانشگاه امیرکبیر در خصوص مزیتهای رقابتی طرح خاطرنشان کرد: سختی بسیار بالا و قابل مقایسه با الماس، چقرمگی شکست بالا که نیاز به زمینههای فلزی را از بین میبرد و دوام و شوکپذیری حرارتی بسیار بالا که امکان تراشکاری بدون نیاز به خنک کننده را فراهم میکند، از مزیتهای رقابتی این طرح به شمار میروند.
گفتنی است؛ این طرح با راهنمایی نادر پروین، دانشیار دانشکده مهندسی مواد دانشگاه صنعتی امیرکبیر و مهدی شاهدی اصل، دانشیار دانشگاه محقق اردبیلی به نتیجه رسیده است.